Laci és Petrosz óráival a WAMP-on találkoztam először, és egyből megtetszett a letisztult dizájnjuk! Aztán amikor közelebb mentem, láttam, hogy 3D nyomtatással készülnek, akkor el is határoztam, hogy írok erről a zseniális ötletről. Remélem, nektek is tetszeni fog.
Hogyan jutott az eszetekbe ez az egész?
Tíz évvel ezelőtt faliórákat készítettem fából, ami nekem meditáció volt, és egyben hobbi is. Sajnos a munkám miatt nem tudtam már elég időt kint tölteni a műhelyben, de elképesztően hiányzott a kreativitás és az alkotás. Petrosszal nagyon régóta ismerjük egymást, és mondtam neki, hogy én azt vettem a fejembe, hogy egyedi karórákat szeretnék készíteni. Mivel ő építész, remek tervező és piszok kreatív ember, így nem váratott sokat magára a dolog, 2016-ban elindult a projektünk.
Miért pont a 3D nyomtatás lett a megoldás?
Az elején még fa karórákat és a CNC marástechnikát gondoltuk jó megoldásnak. Elkészült az első modell, de folyamatosan falakba ütköztünk a gyártás során. Inkább úgy fogalmaznék, hogy elmentünk tíz szakemberhez, de senki nem akarta még a prototípust sem legyártani. Eközben azért már nézegettük a 3D nyomtatós videókat, blogokat, kezdtünk ismerkedni a technikával.
Modellünk már volt, így elvittük egy csapathoz, akik saját fejlesztésű 3D nyomtatókat gyártottak. Egy hét múlva elkészült az első 3D nyomtatott karóra tok. Ugyan még nem mi nyomtattuk, de elképesztő büszkék voltunk rá. Az elején még klasszik kétrészes szíjban gondolkodtunk, és az ehhez passzoló formákon. Ez akkor változott meg, amikor megvettük a saját nyomtatónkat, és elkezdtünk megismerkedni, kísérletezni vele. 2018-ra elkészült az első olyan prototípus, ami már hordható volt. Készítettünk is a barátoknak, ismerősöknek, akiktől rengeteg hasznos, használható és pozitív visszajelzést kaptunk. Ezekből rengeteget tanultunk, és fel is használtunk.
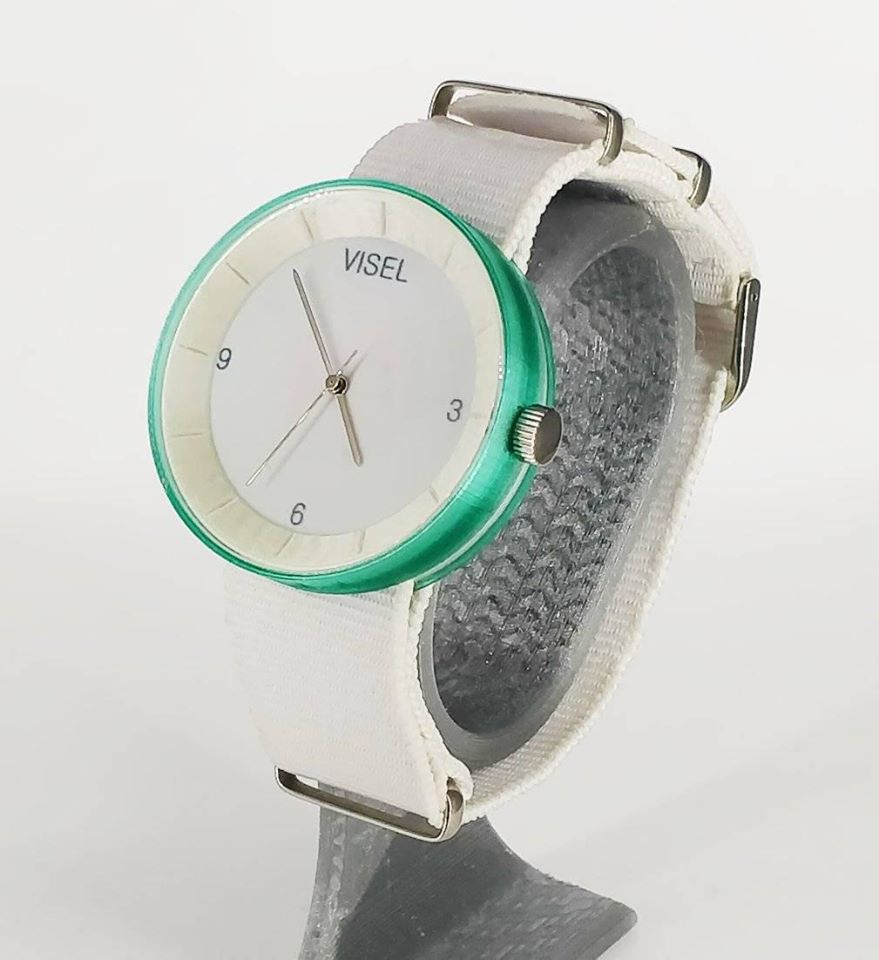
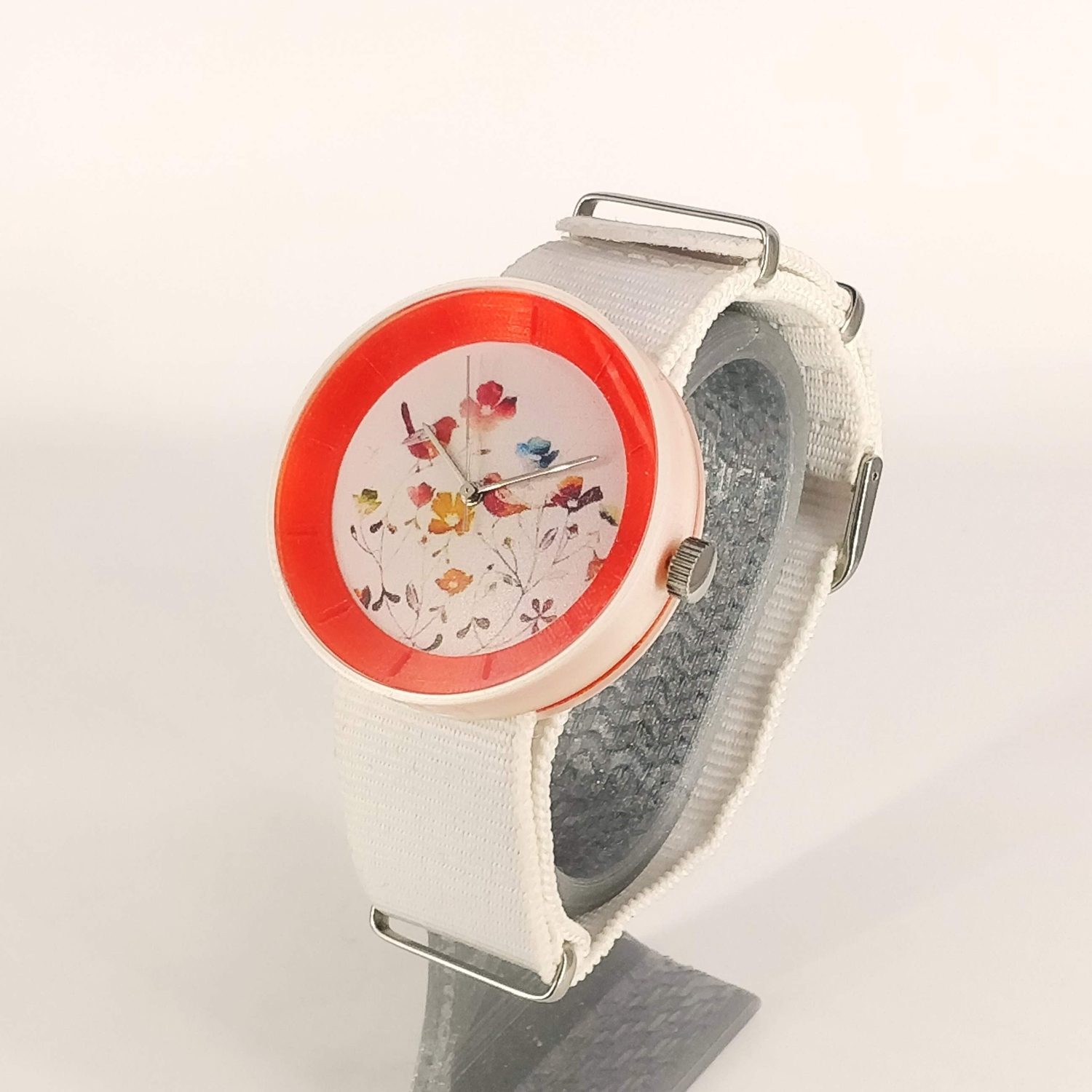
Környezettudatos alapanyagok
A nyomtató alapanyag-választásnál is fontos szempont volt, hogy ne termeljünk felesleges hulladékot. Ez elsődleges kritérium volt a 3D technológia választásánál is, mert hulladék feldolgozással foglalkozom, így a fenntartható hulladékgazdálkodás mindig is nagyon előtérben volt nálam. Az alapanyag PLA, azaz bio műanyag (kukorica keményítőből készül).
Kedvenc alapanyagunk, amivel egy kicsit visszanyúlunk a kezdetekhez (fa karóra), egy speciális bio műanyag és fapor keveréke. Ennek a nyomtatás után igazán fa hatása van, sőt nyomtatás közben (210 fokon) még faillata is van. Fontos megjegyezni, hogy csak speciális körülmények között komposztálható egyelőre, ezért azt tervezzük, hogy azt a kevés hulladékot, amit termelünk, inkább bedaráljuk, és újra alapanyagot készítünk belőle.
UV-nyomtatással készülnek a számlapok
A következő nehézséget a számlapdizájn hozta. Azt, hogy milyen technológiával dolgozzunk, elég gyorsan sikerült tisztázni. Az UV-nyomtatás egy remek technológia, és gyönyörű nyomtatási eredményt kapunk. De az elején sehogy sem jöttek a szép és pontos nyomtatások. Ezért tovább mentem, és sikerült bejutnom az egyik legnagyobb forgalmazó bázisára, ahol láttam, mit is lehet ezzel a technológiával készíteni. Őszintén mondom, nincsenek határok. Na már csak egy olyan embert kellett találni, akinek van ilyen gépe, és ért is hozzá, de meglett. Ákos (a Green Digital Kft. tulajdonosa) nagyon ért ahhoz, amit csinál, és ami még talán ennél is fontosabb, hihetetlen lelkes. Pontos és gyönyörű számlapokat készített nekünk. Ezek után azt mondhatom, hogy 2019 közepére elkészült a Visel Design karóra.
Ki a dizájner közületek?
Az ötletelés közös, de a modelleket és a végleges dizájnt Petrosz készíti el. Sokat tanulok tőle a formákról és az egységről. Kordában tartja azt a rengeteg – és szerteágazó – ötletet, amit folyamatosan rázúdítok.
Az óra melyik részei készülnek 3D nyomtatással?
Az óra öt részből áll. Tok, hátlap, perem, skála, számlap – ezeket nyomtatjuk ki. Még egy alkatrészt nyomtatunk, ez az óraműtartó.
Az óraszerkezet Japán Miyota, ami egy hihetetlen megbízható és elnyűhetetlen szerkezet. A korona és a mutatók Svájcból érkeznek. Az óraüveg pedig kristályüveg, ami komoly igénybevétel esetén is állja a sarat.
Ha valaki egyedit szeretne, az óra melyik részeit tudja saját maga kiválasztani a weboldalatokon?
Van a honlapon egy karóratervező, ahol a tok, a számlap, a hátlap, a skála és a perem színe változtatható. Így vonjuk be az érdeklődőket a tervezésbe. A használata pofon egyszerű, mert rákattintunk az alkatrészre, színskálából kiválasztjuk a színt, és már látjuk is az eredményt. Számlapdizájnban még nagyon sok lehetőséget látok. Az UV-nyomtatással tényleg elképesztő dolgokat lehet készíteni még egy ilyen kis felületre is.
A másik nagy kedvencem a karóraszíj, amiben nagy fantáziát látok. Leginkább az anyagfelhasználásban gondolkodom. Mostanában fedeztem fel a papírtextilt, amivel még kísérleteztek, de látom benne a fantáziát. Természetesen az újra anyagokból készült karóraszíj is nagyon érdekel, és rengeteget kísérletezem ezekkel.
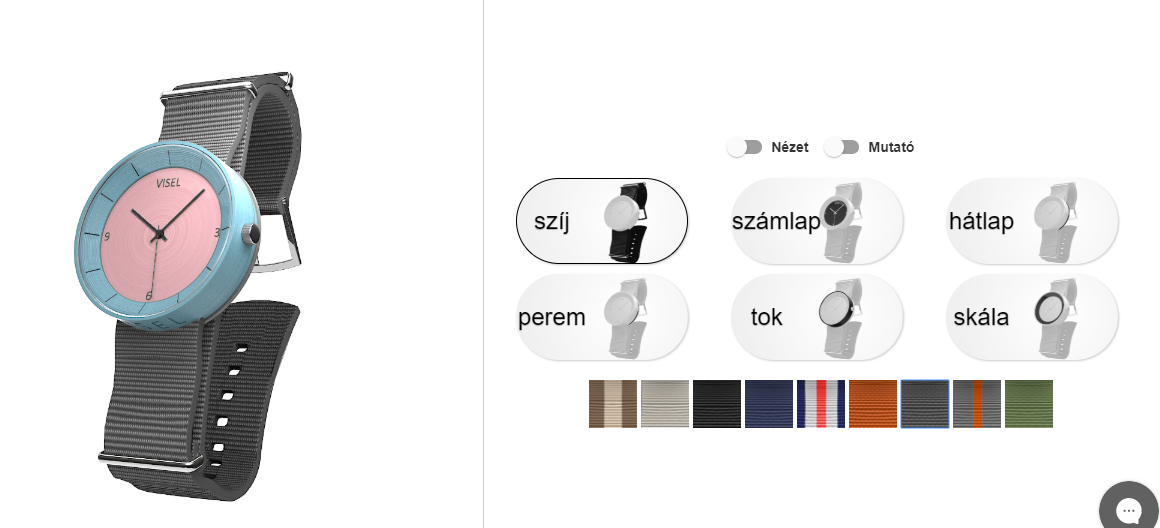
Miért fontos nektek, hogy a 3D nyomtatási technika közelebb kerüljön az emberekhez?
Még a karóra gyártása előtt az első gondolat, ami megfogalmazódott bennem, hogy egyedi modelleket és nyomtatásokat szeretnék készíteni. De a honlapra nem azt szeretném kiírni, hogy mi milyen profi módon tervezünk és nyomtatunk. Inkább készítsünk egy terméket, ami mindezt bebizonyítja. Az már csak egy remek dolog, hogy ez a termék tetszik másoknak is, és lett belőle egy eladható termék.
Szóval ha minél többen ismerik a technológiát és azt, hogy mire képes, akkor tudnak ezzel együtt gondolkodni. Egy-egy problémánál eszükbe jut, hogy ezt lehetne modellezni, kinyomtatni és megnézni az eredményt, azon gyorsan változtatni és megkapni a végleges változatot.
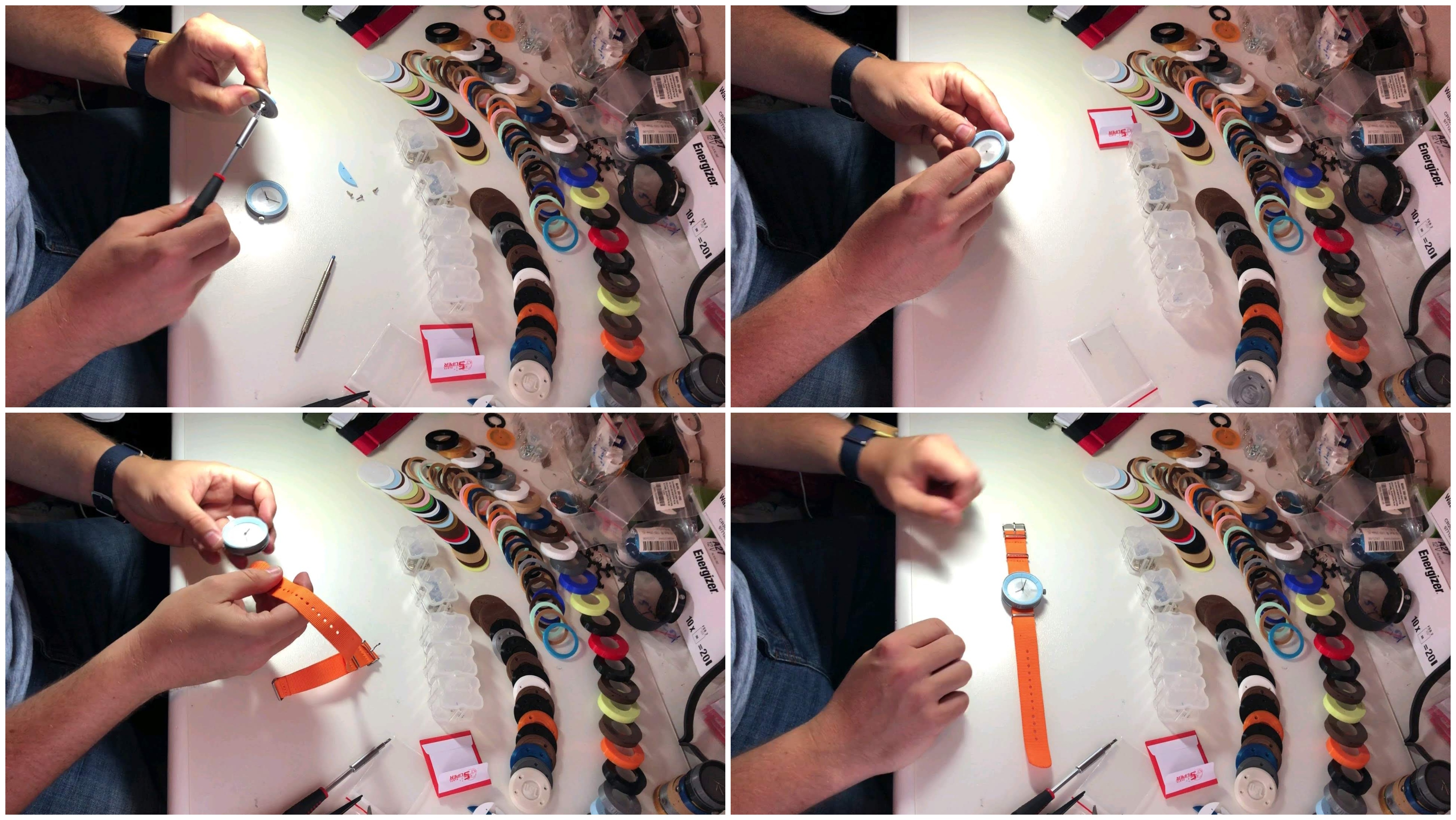
Mennyi idő, mire elkészül egy óra, és mi a folyamata? Biztosan sokakat érdekel, hogy kicsit belássanak a kulisszák mögé!
Összesen, ha minden alkatrészt egyszerre szeretnénk kinyomtatni, akkor három óra a nyomtatási idő. Ez nem túl jó hír, ha azt nézem, hogy egy nyolcórás munkaidőben csak két órát tudunk elkészíteni. Egy képzés alkalmával találkoztam a lean menedzsmenttel, ami nagyon sokat segített, hogy ezen javítsunk. Ezt úgy értük el, hogy a két nagy alkatrészből (tok, hátlap) tartunk kisebb készletet. Minden színből két darabot. A számlapok előre ki vannak nyomtatva, mert azokra UV-nyomtatással kerül fel a dizájn. Így a perem és a skála nyomtatása közben (kb. 30 perc) a tokba belerakom az óraművet, beragasztom a számlapot, és felteszem a mutatókat. A skálát a helyére illesztem, és az óraüveget beragasztom. A végén négy csavarral a hátlapot és a peremet rögzítem a tokhoz. Átfűzöm a szíjat, és a 3D nyomtatott dobozba teszem az elkészült karórát. 55 perc a három óra helyett. Na ez így már jobban hangzik!